Dyno Nobel’s DynoConsult team and electronic detonators recently helped bring a midwestern North American coal mining customer savings of more than $100,000 per ramp shot as it implemented a new ramp design.
Optimized blast timing can certainly lead to savings – but $100,000 per ramp shot? According to a recent customer study, it is possible, and it is already leading to even more savings for the mine’s haul fleet.
The midwestern surface coal operation needed to implement a new ramp design to reduce the haul distance for removal of surface dirt. The ramp would be constructed using material from their uppermost rock bench; this rock is typically cast into the pit bottom, leaving a small muck pile remaining on top of the highwall.
It was determined the volume of the remaining non-cast material was not sufficient for the construction of the ramp. The customer implemented a new timing scheme to reduce the casting effect, but the volume of material was still insufficient for ramp construction. As another blast was already loaded, DynoConsult was asked to provide timing for the next experimental blast that would reduce the total cast.
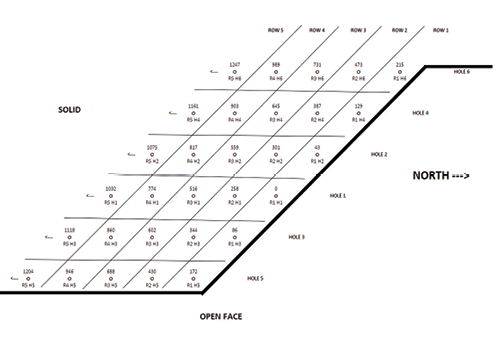
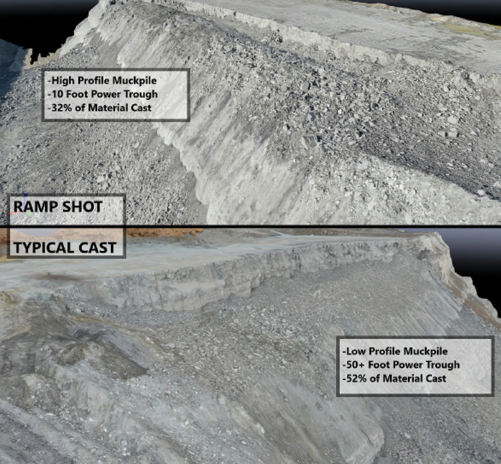

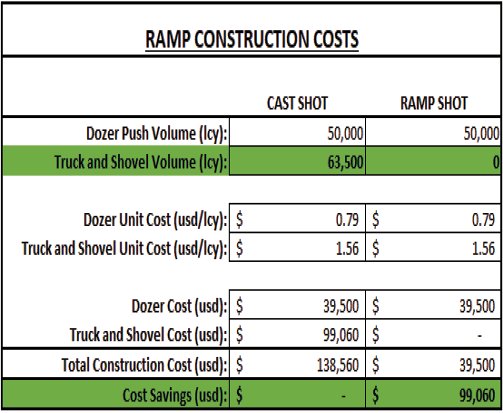
Goals
The primary goal of the ramp blast was a reduction in total cast, and the secondary goal was to shape the muck pile such that the power trough was minimal and the crest of the muck pile was level with the bench surface. The coal mine’s ramp blast was designed as a square pattern with six rows of 22 holes on an echelon with burden and spacing of 20 feet by 34 feet, a design typical of the cast blasts used at the mine site.
Because the ramp blast was already drilled and loaded, blast timing was the only viable method to change the blast outcome.
The site used the DigiShot electronic initiation system, and all blasts were timed by inputting a hole-to-hole and row-to-row timing. Due to time constraints, the customer requested a simple tagging and timing scheme. Previous blasting experiments in similar rock found that a 43-millisecond regular rhythmic timing reduces total movement in a casting environment.
The DynoConsult team theorized that the best way to reduce the total cast of the shot without causing excessive burden or dead-pressing was tagging the ramp blast as a 22-row by six-hole blast with the effective burden following the echelon angle. To reduce the power trough and keep the material from casting into the pit, the timing was designed to pull to the center.
Bringing in the tech
The customer’s primary goal of reduced total cast for ramp blasts and secondary goal of shaping the muck pile in a way that allows for efficient construction of a ramp using the non-cast material, required accuracy and precision. As seen in Figure 2, the crest of the muck pile is nearly level with the remaining bench, and the power trough is over 40 ft. shallower than the typical cast.
The customer considered this the best outcome, with the bulldozer fleet doing minimal prep work before being able to construct the ramp. Without electronic detonators, this outcome would be significantly more difficult to achieve, noted Dyno Nobel, as the precision timing required to maintain the desired timing contours is only possible with single millisecond-level accuracy.
Given the time constraints for the ramp blast, the crew needed a simple way to tag and program the detonators to prevent any delays in the pit. Because of the simplicity of changing the timing of an electronic blast, there were no unscheduled delays associated with changing the timing for the ramp shot.
Money in pocket
Following initiation of the blast, customer drone footage showed far less material casting into the pit than is typical. A post-blast aerial survey of the blast site provided the data necessary to quantify the visual difference seen in the initial drone footage.
The key performance indicator for the ramp blast was non-cast percentage. The timing achieved the goal of retaining more material within the initial boundaries of the blast, with the non-cast percentage rising from an average of 52.3% to 67.7% for the ramp shot.
By utilizing the specialized timing developed by DynoConsult, the customer saves approximately $100,000 per ramp shot compared to building the ramp using material from a typical cast shot. This is because due to the lack of sufficient non-cast material in a typical cast blast, any additional material needs would require a truck and shovel unit in the pit.
This would add approximately $100,000 to the construction costs and does not generate any cost savings when it comes time to remove the ramp. These savings are realized in every 150 ft. cut at the coal mine.
Following the successful test of the ramp blast timing, the customer implemented the design for successive cuts in the pits where they intended to use a temporary ramp. The simple change to the tagging and timing of the blast proved successful and led to a permanent change in the way the customer shoots their ramp blasts.